Express Newark’s Keary Rosen Uses 3D Printers to Make PPE for NJ's Health Care Workers
Keary Rosen, founding director of the Form Design Studio and Lab at Express Newark, has turned to technology to help make face shields to support New Jersey’s health care workers. Rosen is using fused deposition manufacturing (FDM) 3D printers to produce face shields inside the lab to augment much-needed personal protective equipment (PPE) during the COVID-19 pandemic.
“Every day since April 19, I’ve been printing face-shield visors and chin pieces nonstop,” said Rosen. “I’m essentially going through the lab’s reserve spools of PLA (polylactic acid) filament to make as many visors as possible. The lab has a total of 13 3D printers. I’ve been using seven to eight of them to print PPE.”
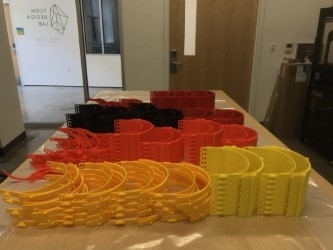
FDM printers use a continuous thermoplastic filament, like PLA, which gets heated to its melting point and then extruded, layer by layer, Rosen explained. “You put a design or model in the computer. The computer communicates with the printer. The printer then extrudes or forces out the molten PLA, one layer after another, until the object is formed.”
“It takes a little more than two hours for one printer to produce a visor,” Rosen estimated. “I’ve probably printed around 50 face-shield visors each day, totaling approximately 350 so far.”
Rosen got the idea to use 3D printing to make PPE when models for face shields started appearing online. “I wanted to help address the shortage of PPE. A face shield is the first line of defense and probably the safest thing to do right now.”
Concerned with creating a safe product, Rosen began experimenting with some of the models he saw online. He also conducted research and read feedback from medical professionals as to comfortability and preferences.
“My foray into 3D printing of PPE became formalized when Peter Englot, senior vice chancellor for public affairs and chief of staff at Rutgers-Newark, invited me to join the Rutgers 3D Printing PPE Initiative,” shared Rosen. Rutgers Business School supply chain management professor Kevin Lyons, who is helping coordinate Rutgers supply chains in response to the pandemic, facilitated that connection. The initiative falls under the purview of the Rutgers COVID-19 Task Force and consists of representatives from all four chancellor-led units: Rutgers University–Newark, Rutgers University–New Brunswick, Rutgers University–Camden, and Rutgers Biomedical and Health Sciences.
VIDEO: Keary Rosen explains how he prints and assembles PPE made at Express Newark.
“The Rutgers COVID-19 Task Force created the 3D Printing PPE Initiative to ensure the quality and safety of all products carrying the Rutgers brand,” said Rosen, noting that the initiative is using a slightly modified version of the Prusa Research design approved by the National Institutes of Health for face shields.

The initiative also handles the supply-chain logistics of product dissemination. To date, the Rutgers 3D Printing PPE Initiative has distributed PPE to emergency departments of RWJBarnabas Health, starting with Robert Wood Johnson University Hospital New Brunswick, and to one hospital in Wall, New Jersey.
“In so many ways it is fitting that Express Newark serves as a site for the production of PPE for our frontline heroes during the pandemic,” remarked Rosen. Express Newark, which opened its doors in January 2017, was created as a “Third Space” where the surrounding Rutgers-Newark community could convene “on equal footing to incubate talent, cultivate engaged scholarship, and promote social practice.”
“Yes, it is true that Express Newark’s Form Design Studio and Lab exist to ‘capture the vision of designers, educators, researchers, manufacturers, amateur inventors, and the overall curious through the use of 3D modeling, scanning, and printing technology.’ But they also exist to turn vision into reality and, whenever possible, use digital design and fabrication to actually improve society.”
In addition to his role as director of Express Newark’s Form Design Studio and Lab, Rosen is a sculptor and faculty member in the Department of Arts, Culture and Media of Rutgers-Newark’s School of Arts and Sciences.
“Teaching digital design and fabrication to the Newark community is the most satisfying teaching I’ve ever done. I enjoy the diversity of people with whom I work -- varying ages, ethnicities, skill levels, professional and artistic backgrounds, etc. -- and am determined to expose as many people as possible to the technology.”